1.泌水
一、概述
簡(jiǎn)單地說(shuō),混凝土是由水泥、粗骨料、細骨料和水拌合而成,在這些組分中,水的比重最小,因此在混凝土澆筑過(guò)程中,當其他組分沉降時(shí),水不斷向上遷移,有些能到達混凝土表面并溢出,有些不能到達表面,這就是泌水。這個(gè)過(guò)程會(huì )一直持續,直到混凝土不再沉降。
二、泌水對混凝土質(zhì)量的影響
如果泌水的速度與混凝土表面水蒸發(fā)速度相同,泌水是無(wú)害的?;炷恋暮繉τ诒WC和易性提高施工性是十分必要的,如果混凝土在澆筑后多余的水分能通過(guò)泌水溢出,可以降低水灰比,提高混凝土的密實(shí)度?;炷辽刑幱谒苄噪A段出現的早期泌水對混凝土并沒(méi)有什么傷害,這時(shí)的混凝土還處在沉降和振搗階段。如果混凝土已經(jīng)失去塑性開(kāi)始初凝,這時(shí)的泌水就會(huì )混凝土的性能產(chǎn)生負面影響。
總的泌水量與混凝土配合比密切相關(guān),特別與用水量、細顆粒含量(水泥、粉煤灰等礦物外摻料、細骨料等)有關(guān)。用水量越大,泌水量也越大;細顆粒含量越多,泌水量越小。泌水量還與混凝土的澆筑厚度有關(guān),厚度越厚,泌水越多。
一般情況下,泌水在整個(gè)混凝土表面均勻出現。但在某些特殊情況下,如果混凝土內部有垂直的泌水通道,水在這些通道中向上遷移的速度很快,有可能將一些細顆粒帶出,在內部留下“蟲(chóng)眼”,在表面形成“砂條”。這些泌水通道通常是由于泌水量過(guò)大造成的。泌水通道在混凝土表面留下了敞開(kāi)的路徑,使得化冰鹽等腐蝕性物質(zhì)輕易就能進(jìn)入混凝土內部,導致混凝土出現鋼筋銹蝕、耐久性下降等病害。
在泌水過(guò)程中,水有可能被扁平或片狀的骨料及鋼筋滯留,在這些骨料或鋼筋下面形成積水,就會(huì )形成所謂的“內泌水”。這些內泌水最終也可能從表面泌出,在混凝土表面形成積水。被滯留在骨料或鋼筋下面的內泌水會(huì )使局部水灰比加大,影響水泥石與骨料和鋼筋的粘合強度,形成脆弱的結合面,在受到水化熱、干縮等因素引起的張應力作用下,容易出現微開(kāi)裂。在結構服役過(guò)程中,受到荷載的影響,這些微開(kāi)裂會(huì )逐步加劇,直接影響混凝土結構的安全和耐久性。
表面泌水會(huì )使得混凝土表面的密實(shí)度下降,抗摩擦能力下降。如果在表面泌水還沒(méi)有完全蒸發(fā)就進(jìn)行抹平和收光,會(huì )將泌水重新壓回混凝土表層,加大表層水灰比,使表層強度下降,容易誘發(fā)塑性開(kāi)裂、干縮開(kāi)裂,影響混凝土的耐久性,同時(shí)還可能造成混凝土表面出現氣泡、起皮、起砂等現象。因此,一定要在泌水出現前先將混凝土表面大致抹平,待泌水徹底蒸發(fā)后再進(jìn)行收光。
泌水還會(huì )使水平施工縫處積聚大量的水泥漿,在施工縫處出現強度很低的結合層。
三、混凝土組分對泌水的影響
1,水灰比:水灰比越大泌水越多,用水量增加20%,泌水量可能增加2到3倍。
2,水泥:水泥的種類(lèi)、細度和用量都會(huì )影響泌水。水泥越細,泌水量越少;水泥用量越大,泌水量越少。因此,增加水泥用量,降低水灰比,可以減少泌水。
3,礦物外摻料:粉煤灰、礦渣、硅粉以及天然火山灰等礦物外摻料可以減少泌水,特別是硅粉,對于減少泌水效果十分明顯。因此對硅粉混凝土要加強早期養護,防止出現塑性干縮開(kāi)裂。
4,骨料:骨料的含泥量越高,泌水越少。但含泥量高會(huì )對混凝土其他性能產(chǎn)生負面影響,如加大需水量,增加收縮率等。
5,化學(xué)外加劑:引氣劑可以減少泌水。減水劑也會(huì )減少泌水。
四、降低泌水的措施
1,改善混凝土的配合比;
2,充分攪拌混凝土;
3,使用礦物外摻料;
4,改善骨料的級配;
5,提高水泥基材料的用量;
6,選擇顆粒較細的水泥;
7,使用引氣劑;
8,防止過(guò)振,過(guò)振會(huì )加大泌水;
2、離析
一、什么是離析?
混凝土的離析是指混凝土中的粗骨料沒(méi)有被細骨料和水泥漿均勻、充分地包裹,混凝土硬化后質(zhì)地不均勻。離析有兩種類(lèi)型,第一種是混凝土在塑性狀態(tài)時(shí),粗骨料從混凝土拌合物中分離出來(lái)。第二種是水泥漿從混凝土拌合物中分離出來(lái)。
二、混凝土離析的成因
混凝土是骨料、水泥、水和外加劑的混合物,這些成分的大小和比重各不相同,比如骨料的比重通常為2.6到2.7,而大部分水泥的比重為3.1到3.2。大小和比重的差異使這些成分具有相互分離的傾向。如果在生產(chǎn)和施工過(guò)程中出現失誤,就會(huì )產(chǎn)生離析現象。
離析的主要成因包括:
1,骨料級配不合理和用水量過(guò)大是導致離析的最主要原因。
2,混凝土配合比不當,膠凝材料太少不足以將粗骨料充分包裹,導致粗骨料沉降出現離析。
3,混凝土攪拌不充分。
4,在施工過(guò)程中混凝土垂直落差太大導致離析。
5,現場(chǎng)攪拌混凝土時(shí),如果攪拌機質(zhì)量不好或葉片磨損嚴重,容易導致混凝土離析。
6,大塌落度混凝土或泵送混凝土如果過(guò)振或振搗棒使用不當都會(huì )導致離析。
7,混凝土澆筑后馬上進(jìn)行表面抹平和收光作業(yè),可能會(huì )導致粗骨料沉降,水泥漿上浮,從而導致離析。
8,配筋過(guò)密容易導致離析。
三、防止混凝土離析的措施
1,優(yōu)化混凝土的配合比,提高混凝土的內聚性。如降低水灰比、增加膠凝材料的用量、摻加粉煤灰、硅粉等礦物外摻料等。
2,加強對運輸、澆筑、振搗等施工環(huán)節的質(zhì)量控制。
3,使用引氣劑可以在不犧牲和易性的前提下減少用水量,從而減少離析和泌水。
4,澆筑混凝土時(shí),避免混凝土從高處自由落下,垂直下落的距離越短越好。
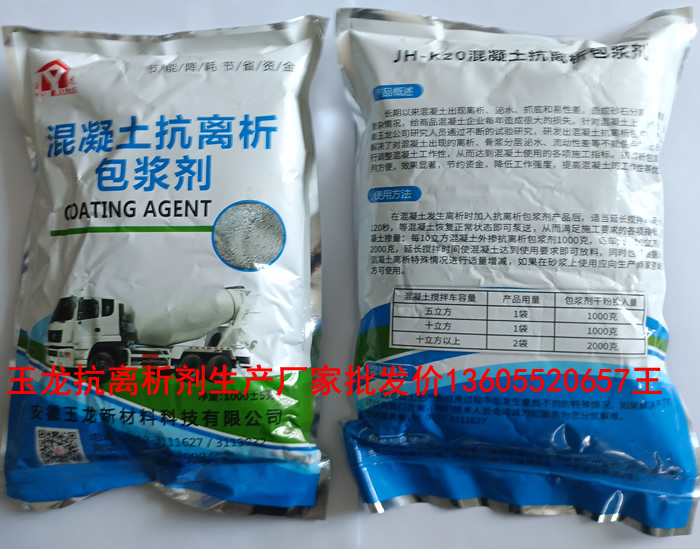
管理員
該內容暫無(wú)評論